- Home
- »
- Fibergrating's Blog
- »
- Manufacturing Processes of Fiberglass Handrails
Table of Contents
Introduction
Fiberglass handrails are widely recognized for their strength, durability, and resistance to corrosion, making them a preferred choice in industrial, commercial, and public infrastructure projects. This article explores the various manufacturing processes involved in producing these high-performance handrails. From traditional techniques like pultrusion and hand layup to modern advancements in automated fiber placement, each method offers unique advantages tailored to specific applications. Additionally, we will discuss how manufacturers are embracing sustainable practices to reduce environmental impact through the use of recycled materials and bio-based resins.
Pultrusion
Pultrusion is a highly efficient process in which continuous strands of fiberglass are pulled through a resin bath and a heated die to achieve the desired shape. This method produces fiberglass handrails that are exceptionally strong, corrosion resistant, and impact resistant. Pultruded fiberglass, for instance, matches the strength of steel grating while eliminating the risk of corrosion.
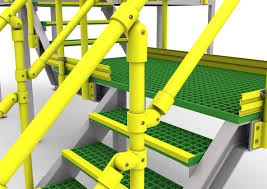
Hand Layup and Open Mold Process
The hand layup process, an open mold technique, involves manually applying layers of fiberglass and resin onto a mold. Although labor-intensive and highly reliant on worker expertise, this method is ideal for producing low volume, large scale items such as tanks or vehicle components. Open molding, one of the oldest techniques, requires minimal technical equipment, making it a good choice for custom or intricate shapes.
Automated Fiber Placement and Tape Laying
Recent advancements have introduced automated techniques like Automated Fiber Placement (AFP) and Automated Tape Laying (ATL) in fiberglass handrail production. These processes offer improved precision and efficiency, especially for complex handrail designs. By reducing labor needs, AFP and ATL enhance the consistency and quality of the finished products.
Sustainability and Environmental Considerations
In light of growing environmental awareness, manufacturers are increasingly using recycled materials in fiberglass handrails to reduce production impact. Moreover, bio-based resins derived from renewable resources such as plants and trees are being explored as eco-friendly alternatives to conventional petroleum based resins.
Contact Us
We value your inquiries and are here to assist you. Whether you have questions about our products, need technical support, or would like to request a quote, please don’t hesitate to reach out to us.
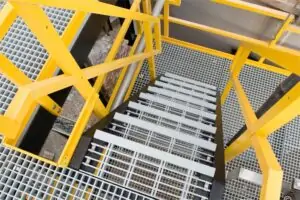
Comments
Frequently Asked Question
Pultrusion is a manufacturing process where continuous strands of fiberglass are pulled through a resin bath and heated die to create the desired shape. This method produces fiberglass handrails that are strong, corrosion-resistant, and impact-resistant, offering the durability of steel without its susceptibility to corrosion.
The hand layup process is an open mold technique where layers of fiberglass and resin are manually applied. While labor-intensive, it’s ideal for producing custom, low-volume, and large-scale products like tanks or vehicle components. It requires less technical machinery but relies heavily on the skill of the worker.
Automated Fiber Placement (AFP) and Automated Tape Laying (ATL) provide greater precision, efficiency, and consistency in manufacturing complex fiberglass handrails. These automated technologies reduce labor costs and enhance the accuracy and uniformity of the final products.
Yes, manufacturers are increasingly adopting sustainable practices by incorporating recycled materials into fiberglass handrails. Additionally, bio-based resins derived from renewable resources like plants and trees are being explored as eco-friendly alternatives to petroleum-based resins, reducing the environmental impact of production.